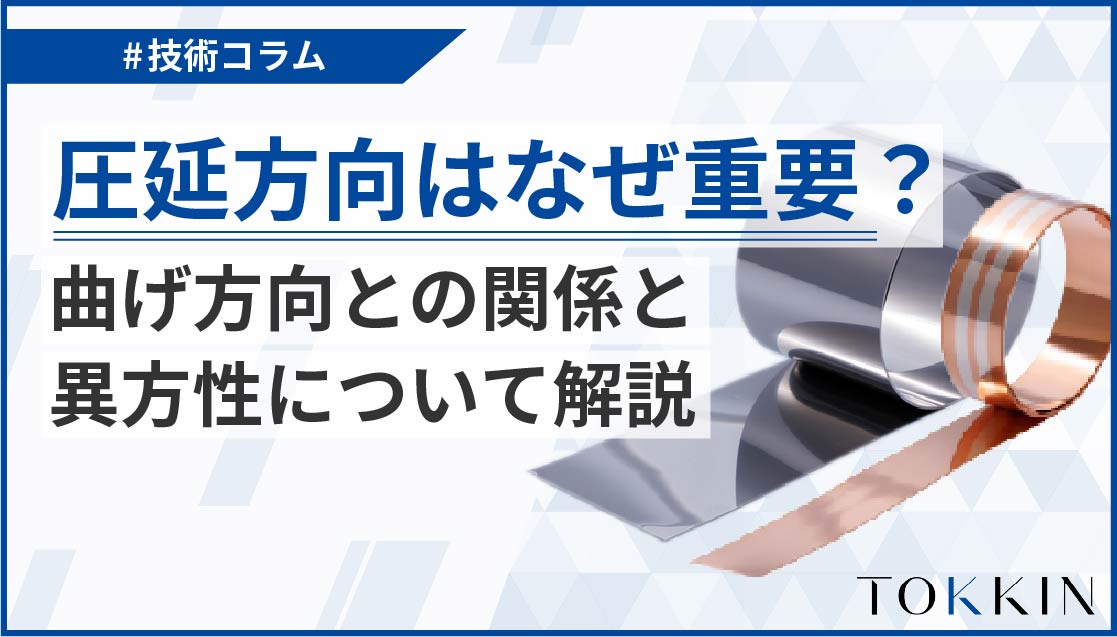
圧延方向はなぜ重要?曲げ方向との関係と異方性について解説
この記事では、高強度なのに高延性を併せ持つ
高強度高延性ステンレス鋼 TOKKIN 350 JIN をご紹介しています。
当社材の用途の中でも特に多い薄板ばねの多くは曲げ加工による成型があり、ばねとしての必須特性である高強度と曲げ加工性のバランスで悩まれるお客様が多くいらっしゃいます。
本記事では、このような課題をお持ちの方向けに、強度と伸びの関係、伸びと曲げ性の関係から、加工限界の最小曲げ半径Rminを事前に予測する方法を解説いたします。
ばねに必要な特性には、「優れた復元力を持つ」「エネルギーの蓄積と放出ができる」「安定した固有振動数を持つ」ことが挙げられます。
この中でも「優れた復元力」は材料強度に大きく依存し、強度が高いほど優れた性能を得ることができます。
日本産業規格(JIS)には「JIS G4313:ばね用ステンレス鋼帯」という規格がありますが、規格名の通り、ばね用途に適したステンレス鋼が規定されており、この規格に規定される鋼種はいずれも加工や熱処理により高い強度が得られる材料となっています。
※JIS G4313で規定されている鋼種:SUS301, SUS304, SUS631, SUS632J1, SUS420J2の5鋼種
この中でも特にオーステナイト系ステンレス鋼のSUS301やSUS304は冷間加工のみで強度が高められ、さらに錆びや変色が発生しにくいことから、分野や国を問わず、ばね用途としてとても幅広く普及しています。
しかしながら、ばねとしての特性を上げようと材料を高強度化すればするほど、曲げ加工などの成型の際に割れやすくなってしまうという難点があります。
本記事では、高強度化したステンレスが割れやすい理由を、強度との伸びの関係、伸びと曲げ加工における最小曲げ半径(Rmin)の関係から解説いたします。
右図にSUS304とSUS301の加工率(圧延率)と機械的性質(硬さ、引張強さ、伸び率)の相関図を示します。
グラフからわかりますように、加工率に比例して強度(硬さ:HV、引張強さ:TS)は増加するのに対し、伸び率(El)は反対に減少します。
このように強度上昇に伴って延性が低下するため、曲げ加工の際に割れやすくなってしまうのです。
ちょこっとメモ
強度上昇に伴い伸び率が低下する現象は、加工(塑性変形)により、転位と呼ばれる原子配列のズレが増加することが理由です。
このメカニズムについては、以下の記事で解説していますのでこちらも併せてご参照ください。
関連記事|加工硬化とは?そのメカニズムや加工硬化曲線の見方について
ここで曲げ加工について少し説明いたします。
そもそも曲げ加工とは何でしょうか。
一般的に物体は応力を加えると変形し、加えた応力を取り除くと元の形に戻ります。もしくは、許容範囲を超える応力を受けると破壊されます。
ところが、金属は一定以上の応力を加えると、応力を取り除いても元の形に戻らずに変形する性質を持っています。
この元に戻らずに変形する性質を「塑性(そせい)」といい、この性質を利用し目的の形状に加工することを「塑性加工」と言います。
塑性加工には、当社のように厚い板をロールで延ばし薄くする「圧延加工」や板状のものを箱や筒のような深さのある形にする「絞り加工」、平たい板を曲げて角度を付ける「曲げ加工」などがあり、金属の薄板ばねにおいては、この「曲げ加工」を用いて成型されることが多くなっています。
では、なぜ金属は応力を取り除いても元の形に戻らずに変形するのでしょうか。
次は金属が持つ「弾性」と「塑性」という性質について説明したいと思います。
金属の「弾性」と「塑性」は、以下のような性質のことを言います。
弾性・・・物体を降伏応力以下の応力で変形させた時に、応力を取り除くと元の形に戻る性質
塑性・・・物体を降伏応力以上の応力で変形させた時に、応力を取り除いても元の形に戻らない性質
弾性と塑性の境界となる降伏応力は、引張試験を行うことで明らかになります。
引張試験を行うと図のような応力-ひずみ線図(S-S曲線)を得ることができますが、ひずみが横に大きく増え始める点が「降伏応力:YS」となり、これ以上の応力を掛けると塑性変形が起こり、応力を取り除いても元の形には戻らなくなるのです。
※応力-ひずみ線図は材料によって形が異なりますが、ここではステンレス鋼で良く使われるオフセット法による降伏応力(耐力)を掲載しています。
応力-ひずみ線図については以下の記事で詳しく説明していますので、併せてお読みください。
関連記事|引張強さとは?引張試験や応力-ひずみ曲線(S-S曲線)の見方について
さらに降伏応力以降も応力を掛け続け引張強さを超えると、塑性変形にも限界が訪れ、材料は破壊(破断)します。この現象が曲げ加工時に発生する、「割れ」や「クラック」となります。
では、実際に金属を成型する場合、どのような条件にすれば割れやクラックが発生しないのでしょうか。
曲げ加工の条件は加工方式によっても異なりますが、ここではボトミング方式(V曲げ)に焦点を絞って説明いたします。
ボトミング方式で加工する際には、主に以下の4つの加工条件が重要となり、誤った加工条件を設定してしまうと、加工不良が発生し、せっかく加工したものが製品にならなくなってしまいます。
横にスクロールしてご覧いただけます。
条件 | 記号 | 説明 | 予想される不具合 |
---|---|---|---|
V幅 | V | 曲げ金型の溝幅 | 溝幅が狭いと表面疵が発生しやすくなる |
フランジ長さ | b | 曲げ加工後の縁の高さ | フランジ長さが短いと角度不良が発生しやすくなる |
曲げ加圧力 | P | 曲げ加工に必要な応力 | 加圧力が小さいと曲げられない |
曲げ半径 | R | 曲げ加工部内側の曲げ半径 | 曲げ半径が小さいほど割れ(クラック)が発生しやすくなる |
では、事前に加工不良が発生しにくい条件を予測することはできないのでしょうか?
実は、これらの条件は一般的には以下の式を用いて事前に算出することができ、この条件に設定することで加工不良を起こさずに、安定した曲げ加工が可能となります。
加工条件の算出方法
t:板厚[mm] V:ダイのV幅[mm]
L:曲げ長さ[m] σ:材料の引張強さ[MPa]
C:補正係数[1.2~1.6]
しかしながら、お客様によってはこの式よりも小さい曲げ半径で加工しなければならないケースがあります。
同じ厚さの材料を曲げる場合、曲げRが小さいほどクラックが発生しやすくなるため、より小さなRで曲げる場合は事前の十分な検証が必要となります。
次では割れを起こさずに加工できる限界の曲げ半径を「最小曲げ半径(Rmin)」と称し、Rminを事前に予測する方法について解説していきます。
ちょこっとメモ
曲げ半径Rの大小による成型後の形状の違いを模式図にしました。
曲げRが小さい方がより緻密で複雑な形状に加工できるようになるため、部品の小型化、省スペース化、低背化が可能となります。
このような理由から、近年、精密ばねの曲げRを極力小さくしたいというご要望が多くなっています。
Rminの予測の前に、金属材料を曲げ加工するとどのように変化するかを知る必要があります。
例えば、金属材料を下図のように曲げると、外側の面は伸び(引張応力)、内側の面は縮む(圧縮応力)ように変形(応力がかかる)し、それぞれ表層部にいくにつれ、引張応力と圧縮応力は大きくなります。
この引張応力と圧縮応力が均等となり、長さ変化が起こらない面を中立面(中立軸)といいますが、この中立面は①板厚が厚い ②曲げ半径が小さい ③曲げる角度が大きい(鋭角である)ほど内側にずれ、引張応力の作用で曲げ部の板厚が減少します。
※一般的に、板厚の減少がなく加工できる曲げ半径は上述のR=5tとなり、R<5tになると中立面がずれて板厚が減少するとされています。
この板厚減少を予測し、曲げ部の最外周長さの変化量を求めることでRminを予測できるようになります。
V曲げの場合、曲げ加工前後の板厚変動比(K)は以下の式で近似できるとされています。
※Kは加工によって板厚がマイナスになったり加工前より厚くなることはないため、0<K≦1.0の範囲となります。
次に、Kを用いて曲げ加工後の板厚(t1)を求めます。
また、中立面までの長さ(t2)は次のような関係となります。
曲げ加工後の板厚t'と中立面までの長さt''が求められたら、次は最外周円弧長さXと中立面円弧長さX'を求めます。
最後にXとX'の差から曲げ加工による伸び率を出します。
この加工による伸び率が材料自体の持つ伸び率よりも大きくなると割れが発生するため、加工による伸び率と材料の伸び率が等しくなる点が加工限界となります。
これまでの式を使用して、板厚0.5mmと1.0mmの90°曲げにおける伸び率Elと最小曲げ半径Rminの関係を表したグラフが下図となります。
赤の曲線が加工限界となり、曲線よりも右上の条件であれば割れの発生確率を下げることができます。
板厚が薄いほど、伸び率が大きいほど、Rminは小さくできるということがわかりますね。
【注意】Rminは材料の表面状態、結晶粒度、バリ方向、曲げ方向や曲げ方式など様々な要因によって変化しますので、この値はあくまで参考値としてご利用ください。データの誤りなどによって生じた損害に対し、当社は一切の責任を負いかねます。
このグラフを用いて、当社の高強度高延性ステンレス鋼「TOKKIN 350 JIN」と同等耐力を持つ「SUS301-EH」を比較してみました。
鋼種 | 耐力YS | 引張強さTS | 伸び率EL |
---|---|---|---|
TOKKIN 350 JIN | 1523 | 1567 | 23 |
SUS301-EH | 1540 | 1740 | 2 |
それぞれの伸び率の位置に線を引いていますが、同じ条件で加工する場合、
TOKKIN 350 JINでは、Rのほとんどの領域で割れの発生確率が低いのに対し、
SUS301-EHでは、R13mm付近で割れ発生の可能性が出てくるということになります。
また、同じ鋼種でも調質によってRminは変わります。
以下にSUS301-HとSUS301-EHの機械的性質の代表値を示します。
鋼種 | 耐力YS | 引張強さTS | 伸び率EL |
---|---|---|---|
SUS301-H | 1240 | 1520 | 17 |
SUS301-EH | 1540 | 1740 | 2 |
この数値をグラフに当てはめると、SUS301-HではRminは1.0程度に対し、
より強度の高いSUS301-EHでは伸び率が低下するため、Rminは右にずれ、R13mm付近で割れ発生の可能性が出てくるということになります。
これまでの説明から、曲げ加工においては、素材の伸び率Elが高いほど最小曲げ半径Rminを小さくできる(割れにくくなる)ことが分かったと思います。
SUS301に限らず、どのような金属材料でも高強度化すると伸び率が低下するため、強度の高い材料は成型加工の際に割れやすくなってしまうのです。
当社では、金属ばねに限らず、高強度を必要とするお客様から曲げ割れや最小曲げ半径Rminのご相談をいただくことが多く、そのようなお客様の声に応えるべく、独自技術により高強度でありながら高い延性を持つ「高強度高延性ステンレス鋼~JIN(ジン)~」を開発いたしました。
JINはこれまでの高強度ステンレス鋼と比較し伸び率が高いため、より小さな曲げRの加工など厳しい条件での成型加工が可能です。また、この材料は高い疲労特性も備えていますのでばね用途には最適な材料です。このようなお悩みをお持ちの方は、ぜひ詳細をご確認下さい。
タグ