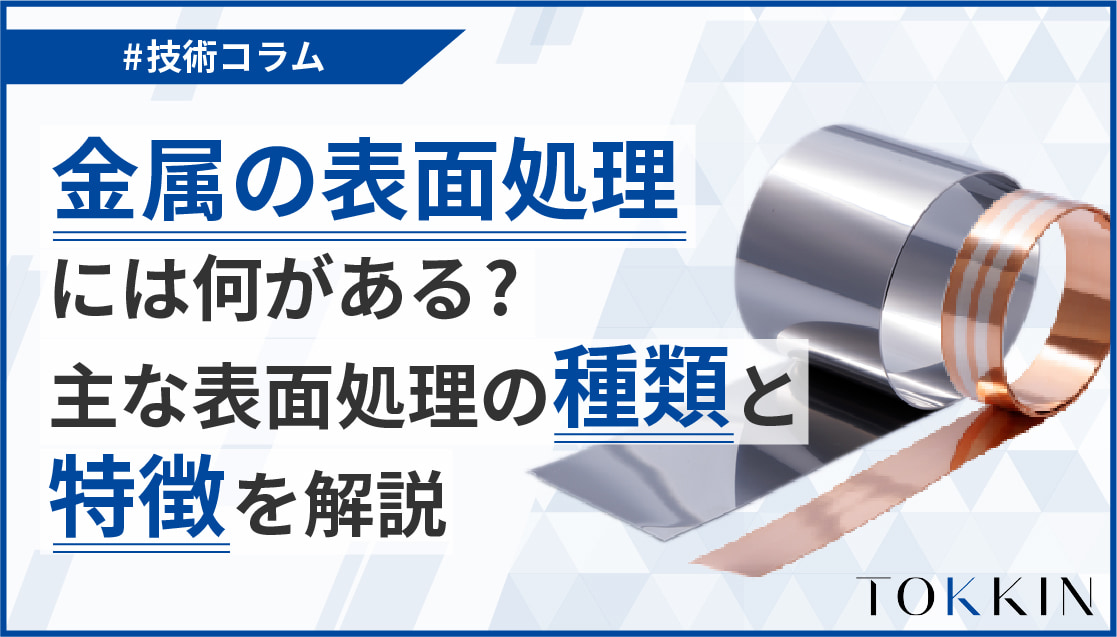
金属の表面処理には何がある?
主な表面処理の種類と特徴を解説
金属材料に関する全60Pの技術資料を無料でダウンロードいただけます。
材料選定に必要な特性データをはじめ、重量・⻑さ換算表や硬さ換算表など金属にかかわる方にオススメのお役立ち資料です。
⇒ 技術資料ダウンロードはこちらから
金属の切削加工とは?
切削加工の種類や、特徴、メカニズム、被削性、被削性指数について解説します。
金属の切削加工とは、工具を用いて金属を切断したり、削ったりするなどして目的の形状・寸法にする加工方法のことです。除去加工の1種であり、切削加工で作られる製品の例としては、シャフト、ノズル、ナットなどが挙げられます。
金属加工の中でも、切削加工はメジャーな加工のひとつであり、自動車や航空機、医療などあらゆる分野で使用される製品にとって欠かせない加工技術となっています。
切削加工の特徴として以下のようなものが挙げられます。
平面、溝、円筒面、穴、ねじなど様々な形状への加工が可能です。
使用する工具等にもよりますが、1μm以下の高い精度での加工が可能です。
金型が不要なためイニシャルコストを抑えることができ、比較的短い納期で生産が可能です。
切削加工は、工具の刃先を工作物に食い込ませ連続的に動かすことで、工作物がせん断変形を起こし、切りくずとして除去されることで行われます。
工具の進行方向にある切り屑をすくい取る面を「すくい面」、切削面から垂直に伸ばした線とすくい面がなす角を「すくい角」といいます。
また、せん断変形が生じる面を「せん断面」、工作物の仕上げ面とせん断面がなす角を「せん断角」といいます。一般に、すくい角が大きくなると、せん断角も大きくなります。
せん断角が大きくなると、工作物の変形量は減少し、切りくずの厚さは薄くなります。
すなわち、切削抵抗が小さくなり、切れ味が向上することを意味します。
そのため、切削加工を行う際は、すくい角を大きくしたり、切削速度を上げるなどし、せん断角を大きくすることが重要とされています。
しかし、すくい角が大きすぎると刃先が細くなり欠けやすくなるため、バランスの取れた角度に調整することも同様に重要です。
切削加工の際に排出される”切りくず”ですが、切削時の刃先の形状や工作物の材質、条件などにより様々な形状に変化します。JISでは以下の4つに大別され、「流れ形」が最も望ましい形状とされています。
切削加工は、以下の3つに大別することができます。
それぞれの加工について、詳しく見ていきましょう。
高速で回転する工作物に工具をあてて、目的の形状に仕上げる加工のことです。一つの刃を持つ単刃工具を使用するため、単刃(たんば)加工とも呼ばれ、基本的に、シャフトやボルトなど円筒や丸型の形状を仕上げる際に使用されます。旋削加工に使用される機械を旋盤、旋盤に使用される工具をバイトといいます。
代表的な旋盤加工として以下のようなものが挙げられます。
回転している工作物にバイトをあてて外周を切削していきます。
旋盤加工の中で最も基本的な加工であり、外丸削りとも呼ばれます。
工作物の先端を円すい状に切削する加工です。
回転している工作物にバイトをあてて、斜めに切削していきます。
回転している工作物にドリルをあてて、穴をあける加工です。
回転している工作物の内側にバイトをあてて削る加工です。
中ぐりとも呼ばれ、一般的に穴あけ加工を施した工作物の穴を広げるように削っていきます。
回転している工作物にバイトをあてて削り、ねじ山を作る加工です。
おねじを作る加工と、めねじを作る加工の2種類があります。
ちょこっとメモ
おねじとめねじとは?
おねじ(雄ねじ):円筒や円錐状の外周に溝を設けたもの
めねじ(雌ネジ):おねじを受け入れるように、穴の内側に溝を設けたもの
固定させた工作物に、高速で回転する工具を押し当てて削る加工です。
一般的には、フライスと呼ばれる円筒面状に多数の刃物を取り付けた工具を用いて加工を行います。一般的には、フライスと呼ばれる円筒面状に多数の刃物を取り付けた工具を用いて加工を行います。
角ばったものや、箱状、板状のものなどの加工に適しており、ミーリング加工とも呼ばれます。
代表的なフライス加工として以下のようなものが挙げられます。
正面フライスと呼ばれる円周上に多数の刃物を取り付けた工具を用いて、工作物の表面を削る加工です。
平面切削、側面加工、段加工等をする際に使用されます。
一度に加工できる面積が広く、加工精度も優れているのが特徴です。
平らフライスと呼ばれる円筒状の外周面に刃をもつ工具を用いて平面を削る加工です。
切削効率に優れていますが、精度は高くないため荒削りなどの加工に適しています。
エンドミルと呼ばれる円柱の外周と端面に切れ刃をもつ工具を用いて、工作物を削る加工です。
側面加工、溝加工、テーパ加工、ポケット加工など様々な加工を高精度で行えるという特徴があります。
外周に刃をもった円盤状の工具である溝フライスなどを用いて溝をつくる加工です。
溝フライスは、長く深い溝加工を行う際に適しており、エンドミルよりも切りくずの排出性に優れています。
使用する工具により、T字型のT溝加工や台形型のアリ溝加工といった形状に加工することも可能です。
工作物を固定し、ドリルと呼ばれる工具で穴を空ける加工です。
穴あけ加工は、主に以下の4つの種類に大別されます。
ドリルを用いて工作物に穴を空ける基本的な加工です。
貫通している穴を貫通穴、貫通させない穴を止まり穴と言います。
ねじやボルトの頭が製品の表面から出てしまうのを防ぐために、工作物にくぼみを作る加工です。
ドリルで開けた穴の精度をあげるために行う加工です。
側面に刃があるリーマと呼ばれる工具を穴に入れ、穴の内側を削ることで公差内の寸法に仕上げます。
ドリルで開けた穴に、めねじのネジ山を形成する加工です。
外周に切れ刃があるタップと呼ばれる工具を穴に入れ、穴の内部を加工します。
切削加工時の材料の削られやすさのことを”被削性(切削性)”といい、被削性を評価する一般的な判断基準として、以下のものが挙げられます。
∟刃物がどれくらい長く使えるか
∟切りくずがスムーズに排出されるか
∟温度が上がりすぎないか
∟削るときにどれくらいの力が必要か
∟仕上面がどれくらい滑らかか
これらの基準には、使用する工具、切削条件、工作物の寸法などさまざまな要因が影響を与えており、”材料特性”もその重要な要因の一つです。
被削性に影響を与える主な材料特性は、以下の通りです。
硬度 | 硬度が高すぎると工具の摩耗が激しくなり、低すぎると材料が刃先に溶着しやすく仕上げ面の精度が低下します。 |
---|---|
靭性 | 靭性が強い材料は、切屑が切りにくく、バリも残りやすくなります。 |
強度 | 強度が高いと変形に必要な力も大きくなり、切削抵抗も高くなります。 |
高温強度 | 高温強度が大きいと、切削熱で被削材が軟化せず切削抵抗も高くなります。 |
加工硬化性 | 加工硬化が大きいと、工具の摩耗も大きくなり寿命が低下します。 |
熱伝導率 | 熱伝導率が小さいと、切削熱が逃げにくく工具の摩耗が大きくなり、寿命も低下します。 |
親和性 | 工具と被削材の親和性が高いと、材料が刃先に溶着しやすくなり仕上げ面の精度が低下します。 |
上述のように被削性には多くの要因が関わってきますので、1つの値だけでは被削性を比較することができません。
そのため、被削性を定量的に表すために「被削性指数」という指標が設けられています。
被削性指数は、硫黄快削鋼の切削性を100として、比較材が同一工具寿命でどの程度切削できたかを表したものとなり、数字が大きいほど切削し易く、数字が小さいほど切削し難いということになります。
以下に主な材料の被削性の位置付けを示します。上述の通り、被削性は材料強度をはじめとする複数の要因の影響を受けるため、この位置付けはあくまで目安となりますこと予めご理解ください。
厚板や丸棒、ブロックなどの大きなサイズの材料は、切削加工で成形することが多く、一般材料では被削性が問題になることがあります。
そのため、一般材料に特定の元素を意図的に添加し、快削性を向上させた鋼種も開発されています。
例えば、硫黄快削鋼では硫黄(S)、快削純鉄では鉛(Pb)、SUS303では硫黄(S)やリン(P)などが快削性のために添加された元素になります。
当社にも切削加工を利用した製品がありますので、少しご紹介いたします。
加工材料の被削性によって対応可否が変わりますので、難切削材のお引き合いの時は都度ご相談とさせていただいています。
スリット加工後のエッジを刃物で切削し、エッジの形状を変えたり、滑らかに整えたりする加工です。
エッジをそのまま使う用途において、平滑性や疲労強度の向上を目的に追加されます。
金属条の表面を切削し、凸型、凹型、階段型のような断面形状にする加工です。
全長にわたって連続した成形がされているため、部品1個1個で加工する必要がなくなります。
上述したように切削性には、様々な材料特性が影響を与えており、
材料選定時に考慮すべき事項が多くあります。
などのご要望やお悩みがありましたら、一度当社にご相談してみませんか?
材料特性、用途、お客様の課題などを考慮し、最適な材料をご提案させていただきます。
ご相談やお見積りは無料ですので、お気軽にご連絡ください。
また、金属材料の特性をまとめた技術カタログを無料で配布しています。
以下より、ぜひダウンロードください。
タグ