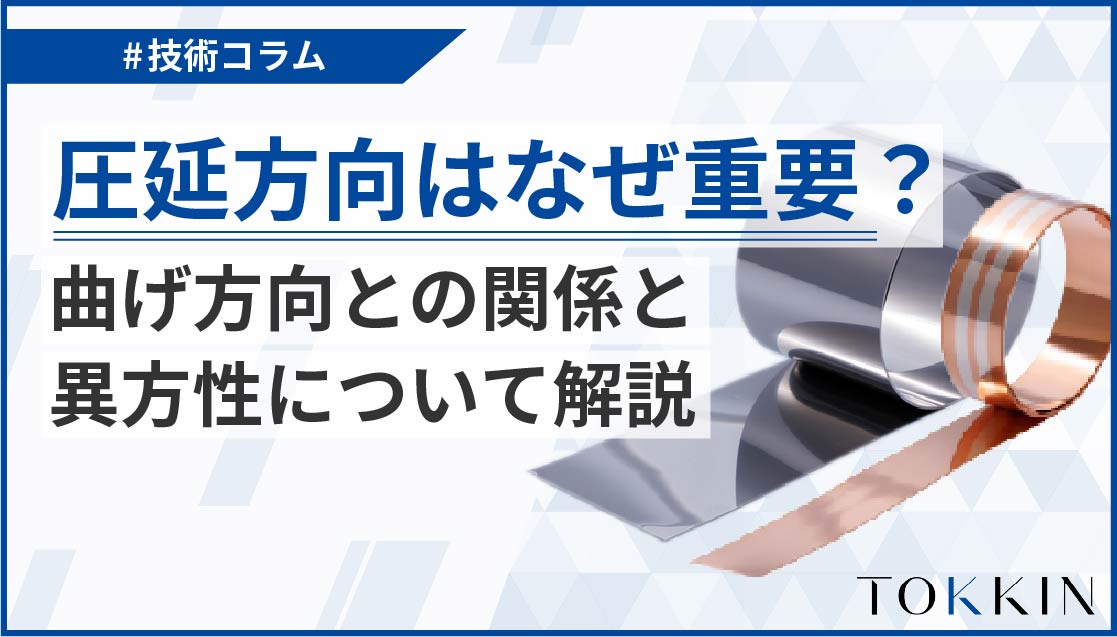
圧延方向はなぜ重要?曲げ方向との関係と異方性について解説
家庭にあるスプーンやフォークなどから、医療機器や航空機部品など幅広い分野で使われているステンレス鋼ですが、その製造工程の大まかな流れは以下の図のようになります。(当記事では、電炉メーカーの工程を元にしています)
当社では、製鋼メーカーで製造された板厚1~3mm程度の原材料を購入し、冷間圧延などの加工を施すことでユーザー様の使い易いサイズや数量で提供しています。
それぞれの工程について、もう少し詳しくみていきましょう。
ステンレスは鉄、クロム、ニッケルを主成分としていますが、その原料である鉄鉱石、石炭、クロム鉱石、ニッケル鉱石等は国内ではほぼ産出されず、その殆どを海外からの輸入に頼っています。また、特にクロムやニッケルは日本ではレアメタルと呼ばれる希少かつ高価な金属として指定されており、価格変動や供給不安のリスクが常にあるのが現状です。
そのため、近年では政府が資源産出国への海外投資やリサイクルシステムの構築と強化を行うなど、安定供給を目指した取り組みが行われています。
鉱石を電気炉にて溶解、精製することでできたフェロアロイ(フェロクロムやフェロニッケルなどの合金鉄)やリサイクル材であるステンレススクラップはステンレスの原材料として製造に使用されます。
これらフェロアロイやステンレススクラップ材は、電気炉に挿入され、溶解されます。この電気炉は、アーク熱により金属を溶かす炉であり温度は3000℃から最大3500℃にも達します。
溶解後は、不純物や炭素を取り除く精錬というプロセスが行われます。ステンレスにおける精錬法の代表的なものとして、以下のAOD法とVOD法があげられます。
ステンレス鋼の精錬プロセスで、高炭素のフェロクロムの配合可能やクロム回収率の向上、極低炭素、不純物減少が大きい特長です。電気炉で原料を溶解後、別の精錬容器に溶湯を移しアルゴン-酸素混合ガスを炉底より吹込み脱炭精錬を行なうもので、酸素のみの吹込みに比べ脱炭反応によって生成するCOの分圧を低くできるので、クロムの酸化損失を押えながら極低炭素まで精錬することができます。
AODと同じような特長をもっていますが、真空タンク中に受鋼した取鍋を入れ、真空中で上吹きランスから酸素を吹込んで脱炭を行なう方法です。量産性ではAODに劣りますが、その真空効果によって極めて低い炭素、窒素、水素の高純度ステンレス鋼の製造に適しております。
なお、精錬後、更に清浄度を高める(不純物を除去する)ために、以下のESRやVARといった再溶解工程を行う場合があります。
溶融スラグの電気抵抗熱により消耗電極を溶解し、水冷銅鋳型の中で凝固させたもので、スラグの精錬作用による脱硫、脱酸や介在物の減少、偏析の少ない健全鋼塊、鋳塊の肌がきれいで、皮ムキをせず熱間加工ができる等の特長があります。
真空または不活性ガス中で素材を消耗電極として直流アークによる溶解を行ない水冷銅鋳型の中で凝固させたもので耐火物の汚染や介在物が極めて少なく、凝固組織の優れた健全な鋼塊が得られます。
消耗電極としては、あらかじめ別の炉(大気溶解炉または真空誘導炉)で成分を調整して電極の形に鋳造したものを使用します。
溶融金属を底の空いた鋳型に長しこみ、底から素材を引き出す鋳造法です。連続的に鋳造をすることができます。連続鋳造法は、以前主流であった造塊ー分塊法(溶融金属を鋳型に流し込み、固めたあとに再加熱してから圧延し、所定の長さに切断する方法)に比べ、工程の省略による生産性向上やコストの低下、さらに品質面においても組織の均一性向上や非金属介在物の減少など多くのメリットがあります。
圧延とは、2本のレールで材料をはさみ圧力によって材料を薄く延ばす加工法で、この工程を経てステンレスとなります。圧延には、主に熱間圧延と冷間圧延の2種類に分けられます。
熱間圧延は900℃~1200℃の高温で加工する方法であり、変形抵抗が小さいため加工性がよい一方、寸法精度が冷間圧延に比べて低く、さらに表面の仕上がりがあまり綺麗でないといった特徴があります。冷間圧延は、常温で圧延加工する方法であり、熱間圧延に比べて加工性は劣りますが、高い寸法精度や滑らかで光沢のある面が得られます。熱間圧延をしてから、より精度の高い冷間圧延で仕上をする場合や、熱間圧延だけを行いそのまま製品になる場合などがあり、用途によって使い分けが行われています。
また、研磨や光輝焼鈍などにより希望の光沢を得る表面仕上げもこの工程で行われます。
当社では上記工程における、冷間圧延や表面仕上げなどの加工を行っています。
当社で取り扱いがあるステンレス鋼の種類、対応可能な調質、表面仕上などについては別のページに詳しい情報が載っていますので、ぜひご確認ください。
また、主な金属の物理的、機械的性質や鋼種の特徴と基本特性などのお役立ち情報が記載されたテクニカルガイドは、以下のフォームよりダウンロード頂けます。
ぜひ、ご活用ください。
タグ